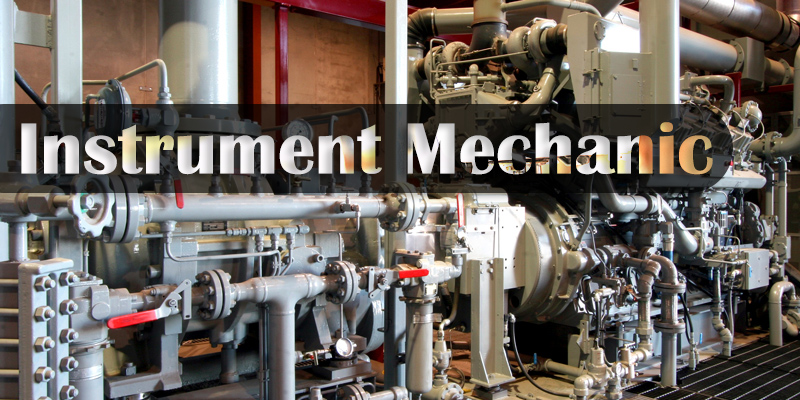
ITI Instrument Mechanic Trade Syllabus
The ITI "Instrument Mechanic" trade is a two-year vocational training program under the Craftsman Training Scheme (CTS), governed by the National Council for Vocational Training (NCVT). This course equips trainees with skills in installing, calibrating, maintaining, and repairing instruments such as pressure gauges, temperature sensors, flow meters, and control systems used in industries like manufacturing, oil and gas, power plants, and automation. The syllabus integrates theoretical knowledge, practical instrumentation skills, and employability skills to prepare students for roles such as instrument technicians, calibration engineers, or maintenance supervisors in industrial setups, or as self-employed service providers for instrumentation maintenance.
Course Overview
- Duration: 2 years (4 semesters, each 6 months)
- NSQF Level: Level 5
- Eligibility: Minimum 10th grade pass with Science and Mathematics (or equivalent)
- Objective: To train individuals in the operation, maintenance, and troubleshooting of industrial instrumentation systems to ensure precision, safety, and efficiency in industrial processes.
Detailed Syllabus Breakdown
1. Trade Theory (Theoretical Knowledge)
Covers principles of instrumentation, electronics, and industrial processes.
- Semester 1
- Introduction to Instrumentation
- Overview: role of instrumentation in industries, career scope.
- Types of instruments: analog, digital, smart instruments.
- Basic concepts: measurement, control, automation.
- Fundamentals of Physics and Mechanics
- Units and measurements: SI units, conversion, accuracy, precision.
- Mechanics: force, pressure, flow, temperature, level.
- Thermodynamics: heat transfer, temperature scales, calibration.
- Electrical Basics
- Ohm’s law, Kirchhoff’s laws, AC/DC circuits.
- Components: resistors, capacitors, inductors, diodes.
- Safety: electrical hazards, grounding, PPE usage.
- Hand Tools and Workshop Practices
- Tools: screwdrivers, pliers, multimeters, soldering irons.
- Workshop safety: handling tools, maintaining cleanliness.
- Basic fabrication: cutting, drilling, filing for instrument mounts.
- Measurement Techniques
- Pressure measurement: manometers, Bourdon tubes, diaphragms.
- Temperature measurement: thermocouples, RTDs, thermistors.
- Flow measurement: orifice plates, venturi tubes, rotameters.
- Calibration Principles
- Calibration: definition, standards, traceability.
- Errors: systematic, random, zero, span errors.
- Tools: deadweight testers, calibrators, reference standards.
- Introduction to Instrumentation
- Semester 2
- Electronics Fundamentals
- Semiconductors: diodes, transistors, ICs, operational amplifiers.
- Circuits: amplifiers, oscillators, filters, power supplies.
- Digital electronics: logic gates, flip-flops, counters.
- Instrument Installation
- Piping and tubing: standards, fittings, leak testing.
- Mounting: sensors, transmitters, control panels.
- Wiring: signal cables, shielding, grounding techniques.
- Level and Flow Measurement
- Level instruments: float, ultrasonic, radar, capacitance types.
- Flow instruments: electromagnetic, turbine, ultrasonic meters.
- Applications: tanks, pipelines, process industries.
- Control Systems Basics
- Open-loop vs. closed-loop systems, feedback mechanisms.
- Controllers: on-off, proportional, PID control.
- Signals: 4-20 mA, 0-10 V, pneumatic signals.
- Maintenance Practices
- Preventive maintenance: schedules, checklists, inspections.
- Troubleshooting: diagnosing faults, signal loss, drift.
- Documentation: maintenance logs, calibration reports.
- Safety Standards
- Industrial safety: hazardous areas, explosion-proof instruments.
- Standards: ISA, IEC, BIS for instrumentation.
- Emergency procedures: handling leaks, electrical faults.
- Electronics Fundamentals
- Semester 3
- Advanced Instrumentation
- Transmitters: pressure, temperature, flow, level transmitters.
- Smart instruments: HART, Foundation Fieldbus, Profibus.
- SCADA systems: overview, data acquisition, remote monitoring.
- Process Control
- Control valves: types (globe, butterfly), actuators, positioners.
- Tuning: PID controller tuning, Ziegler-Nichols method.
- Cascade control: master-slave loops, ratio control.
- Analytical Instruments
- pH meters, conductivity meters, gas analyzers.
- Spectroscopy: UV, IR, mass spectrometry basics.
- Calibration: standard solutions, electrode maintenance.
- PLC Basics
- Programmable Logic Controllers: architecture, I/O modules.
- Programming: ladder logic, basic instructions.
- Integration: interfacing PLCs with field instruments.
- Pneumatic Systems
- Pneumatic instruments: flapper-nozzle, I/P converters.
- Air supply: compressors, regulators, dryers.
- Maintenance: detecting leaks, servicing actuators.
- Industrial Communication
- Protocols: Modbus, OPC, Ethernet-based systems.
- Networking: RS-232, RS-485, wireless communication.
- Data logging: historians, trend analysis.
- Advanced Instrumentation
- Semester 4
- Automation Systems
- DCS (Distributed Control Systems): architecture, applications.
- Industrial IoT: sensors, cloud integration, predictive maintenance.
- Robotics: basics of automated process control.
- Troubleshooting and Repair
- Fault diagnosis: loop testing, signal tracing, root cause analysis.
- Repair techniques: replacing sensors, PCBs, recalibration.
- Case studies: common failures in pressure, flow systems.
- Project Management
- Planning: instrumentation for new setups, retrofitting.
- Costing: budgeting for instruments, maintenance contracts.
- Documentation: P&ID diagrams, loop drawings, SOPs.
- Energy Management
- Energy-efficient instruments: low-power sensors, controllers.
- Monitoring: flow, temperature for energy audits.
- Optimization: reducing losses in process plants.
- Professional Skills
- Entrepreneurship: starting an instrumentation service business.
- Industry trends: AI in automation, smart factories, Industry 4.0.
- Client interaction: preparing bids, technical proposals.
- Environmental and Safety Compliance
- Pollution control: emission monitoring, stack analyzers.
- Safety audits: SIL ratings, intrinsic safety standards.
- Regulations: environmental laws, workplace safety norms.
- Automation Systems
2. Trade Practical (Hands-On Skills)
Focuses on practical instrumentation tasks in workshops and simulated industrial setups.
- Semester 1
- Workshop Practices
- Using tools: cutting, drilling, soldering, crimping wires.
- Measuring: using vernier calipers, micrometers, multimeters.
- Fabricating mounts: preparing brackets, stands for instruments.
- Basic Measurements
- Pressure: calibrating gauges with deadweight testers.
- Temperature: testing thermocouples, RTDs with baths.
- Flow: setting up rotameters, checking readings.
- Electrical Circuits
- Building circuits: series, parallel, using breadboards.
- Testing components: resistors, capacitors with multimeters.
- Wiring: connecting switches, relays in mock panels.
- Calibration Practice
- Calibrating gauges: zero, span adjustments in labs.
- Using standards: reference thermometers, pressure pumps.
- Recording data: preparing calibration certificates.
- Safety Drills
- Handling PPE: wearing gloves, goggles, earplugs.
- Fire safety: using extinguishers, evacuation practice.
- First aid: treating minor shocks, burns in training.
- Project Work
- Assembling a simple instrument: pressure gauge setup.
- Documenting tasks: preparing calibration, maintenance reports.
- Workshop Practices
- Semester 2
- Instrument Installation
- Installing sensors: pressure, temperature in mock pipelines.
- Wiring loops: connecting 4-20 mA transmitters to panels.
- Leak testing: checking tubing, fittings in labs.
- Level and Flow Practice
- Setting up level sensors: ultrasonic, float in mock tanks.
- Calibrating flow meters: orifice, turbine in flow rigs.
- Troubleshooting: diagnosing blockages, signal errors.
- Electronics Practice
- Building circuits: amplifiers, oscillators on PCBs.
- Testing ICs: using logic probes, oscilloscopes.
- Soldering: assembling small control circuits in labs.
- Control Systems
- Setting up controllers: on-off, PID in mock setups.
- Simulating loops: connecting sensors to controllers.
- Tuning: adjusting PID parameters for stability.
- Maintenance Practice
- Inspecting instruments: checking wear, corrosion in labs.
- Cleaning sensors: removing dirt, scaling from probes.
- Logging: updating maintenance records, fault reports.
- Project Work
- Installing a control loop: sensor, transmitter, controller.
- Presenting results: calibration data, loop performance.
- Instrument Installation
- Semester 3
- Advanced Calibration
- Calibrating transmitters: smart pressure, flow devices.
- Using HART communicators: configuring field instruments.
- Testing accuracy: comparing with master standards.
- Control Valve Practice
- Assembling valves: installing actuators, positioners.
- Calibrating positioners: stroke testing, feedback checks.
- Troubleshooting: diagnosing valve sticking, leakage.
- PLC Programming
- Writing ladder logic: basic start-stop, timer programs.
- Connecting PLCs: interfacing with sensors, relays.
- Simulating processes: controlling mock pumps, motors.
- Analytical Instruments
- Calibrating pH meters: using buffer solutions in labs.
- Testing gas analyzers: checking CO, O2 sensors.
- Maintaining electrodes: cleaning, replacing probes.
- Pneumatic Systems
- Setting up I/P converters: converting signals in labs.
- Servicing actuators: checking diaphragms, seals.
- Testing air supply: adjusting regulators, filters.
- Project Work
- Designing a control system: integrating PLC, sensors.
- Documenting setup: preparing loop diagrams, test reports.
- Advanced Calibration
- Semester 4
- Automation Practice
- Configuring SCADA: setting up tags, alarms in labs.
- Testing DCS: simulating process control loops.
- Using IoT: connecting sensors to cloud platforms.
- Troubleshooting
- Diagnosing faults: loop failures, communication errors.
- Repairing instruments: replacing faulty PCBs, sensors.
- Testing repairs: verifying performance post-repair.
- Industrial Communication
- Setting up Modbus: connecting devices in mock networks.
- Testing RS-485: checking signal integrity, termination.
- Logging data: configuring historians for trends.
- Energy Management
- Monitoring flow: using meters for energy audits.
- Optimizing systems: adjusting controls for efficiency.
- Reporting: preparing energy consumption reports.
- Safety and Compliance
- Auditing instruments: checking SIL, intrinsic safety.
- Testing analyzers: calibrating emission monitors.
- Documenting compliance: preparing safety certificates.
- Project Work
- Developing an instrumentation system: for a mock process plant.
- Presenting a portfolio: including P&ID, calibration logs, project report.
- Automation Practice
3. Workshop Calculation and Science
Provides mathematical and scientific support for instrumentation tasks.
- Semester 1
- Arithmetic: calculating errors, signal ranges, calibration points.
- Algebra: solving equations for flow, pressure calculations.
- Science: properties of gases, liquids, thermal expansion.
- Semester 2
- Trigonometry: angles in piping, sensor alignment.
- Statistics: analyzing calibration data, error distribution.
- Science: fluid dynamics, electrical conductivity, heat transfer.
- Semester 3
- Calculus: basics for PID tuning, rate of change in signals.
- Logarithms: used in pH, decibel calculations.
- Science: electrochemistry, optics for analytical instruments.
- Semester 4
- Calculations: budgeting projects, energy consumption analysis.
- Probability: reliability of instruments, failure rates.
- Science: environmental chemistry, energy conservation principles.
4. Engineering Drawing
Focuses on technical drafting for instrumentation systems.
- Semester 1: Sketching basic components, orthographic projections.
- Semester 2: Drawing P&ID, loop diagrams, wiring layouts.
- Semester 3: Designing control panels, instrument mounting plans.
- Semester 4: Creating detailed process flow diagrams, system layouts.
5. Employability Skills
Enhances job readiness and soft skills.
- Semester 1
- Communication skills: reporting faults, writing logs.
- Time management: prioritizing maintenance, calibration tasks.
- Basic IT skills: using Excel, calibration software.
- Semester 2
- Teamwork: collaborating with engineers, electricians.
- Problem-solving: diagnosing instrument failures.
- IT skills: configuring HART, SCADA interfaces.
- Semester 3
- Leadership: supervising junior technicians in labs.
- Negotiation: discussing vendor quotes, service contracts.
- Advanced IT: programming PLCs, networking basics.
- Semester 4
- Entrepreneurship: planning an instrumentation service firm.
- Client management: preparing proposals, technical bids.
- Industry awareness: understanding automation trends, safety norms.
Assessment and Certification
- Examinations: Conducted semester-wise with theoretical and practical components.
- Certification: Successful candidates receive the National Trade Certificate (NTC) from NCVT, recognized nationally and internationally.
- Evaluation: Based on calibration accuracy, troubleshooting skills, system installation proficiency, and project work.
Career Opportunities
- Employment: Instrument technician, calibration engineer, maintenance supervisor in industries like oil and gas, manufacturing, or power plants.
- Self-Employment: Starting an instrumentation calibration or maintenance service.
- Further Studies: Diploma in Instrumentation Engineering, B.Tech in Electronics/Instrumentation, or certifications like ISA-CCST.
Note
- This syllabus aligns with the latest NCVT guidelines and may vary slightly based on institutional or state-specific requirements.
- For the most current version, refer to the Directorate General of Training (DGT) or consult your local ITI.
Trade Type
- 12 views