iti
4 April 2025
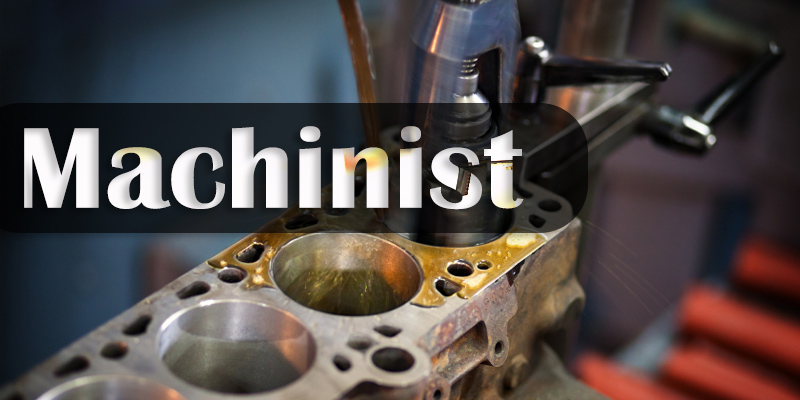
ITI Machinist Syllabus (English)
Course Overview
- Trade Name: Machinist
- Duration: 2 Years (4 Semesters)
- NSQF Level: Level 5
- Eligibility: 10th Grade Pass with Science and Mathematics
- Objective: To train candidates in operating machine tools (lathe, milling, grinding, drilling) to produce precision components, equipping them for roles as machinists, CNC operators, or tool setters in manufacturing, automotive, or aerospace industries, or for self-employment in machining workshops.
- Certification: National Trade Certificate (NTC) by NCVT
Detailed Syllabus
Semester 1
Trade Theory
- Introduction to Machining: Role of machinists, types of machine tools (lathe, milling, drilling), industrial applications.
- Safety Practices: Machine safety, PPE (goggles, gloves), fire hazards, first aid, workshop ergonomics.
- Workshop Tools: Vernier calipers, micrometers, gauges, files, hacksaws; usage and maintenance.
- Lathe Machine Basics: Parts (bed, headstock, carriage), types (center, turret), chucks, and accessories.
- Cutting Tools: High-Speed Steel (HSS), carbide tools, tool geometry, sharpening methods.
- Materials: Ferrous (steel, cast iron) and non-ferrous (aluminum, copper) metals; properties and machining.
- Engineering Drawing: Orthographic projections, blueprints, machining symbols, tolerances.
Trade Practical
- Safety Drills: Using PPE, practicing machine shutdown, handling minor injuries.
- Tool Handling: Measuring with vernier calipers/micrometers, filing flat surfaces, sawing metal bars.
- Lathe Setup: Mounting workpieces in chucks, aligning tools, setting spindle speeds.
- Basic Lathe Operations: Facing, plain turning, step turning, chamfering on mild steel.
- Measurement Practice: Checking workpiece dimensions, ensuring tolerances (±0.05mm).
- Drawing Interpretation: Reading simple machining drawings, marking workpieces for cutting.
- Project Work: Machining a mild steel component (e.g., shaft) with facing and step turning.
Hours: Theory: 160 hours | Practical: 240 hours
Semester 2
Trade Theory
- Milling Machine Basics: Types (horizontal, vertical), parts (table, spindle), cutters (end mill, side-and-face).
- Drilling Machine: Types (bench, radial), drill bits, reamers, tapping; operations and speeds.
- Lathe Operations: Taper turning, thread cutting, knurling, boring; techniques and calculations.
- Cutting Fluids: Types (oil-based, water-based), functions, application in machining.
- Heat Treatment: Annealing, hardening, tempering; effects on machinability.
- Jigs and Fixtures: Purpose, types, design basics for machining accuracy.
- Quality Control: Inspection methods, surface finish standards, ISO tolerances.
Trade Practical
- Milling Operations: Setting up milling machines, machining flat surfaces, slots on mild steel.
- Drilling Tasks: Drilling holes, reaming, tapping threads, counterboring on metal blocks.
- Advanced Lathe Work: Cutting V-threads (metric/BSW), machining tapers, knurling patterns.
- Coolant Use: Applying cutting fluids during milling and drilling, maintaining flow.
- Jig Setup: Using simple jigs for repetitive drilling, ensuring alignment.
- Inspection: Measuring machined parts with gauges, verifying surface finish.
- Project Work: Producing a component (e.g., keyway block) using lathe and milling operations.
Hours: Theory: 160 hours | Practical: 240 hours
Semester 3
Trade Theory
- Grinding Machine Basics: Types (surface, cylindrical), grinding wheels, dressing, balancing.
- Shaping and Slotting: Shaper machine, slotter, tools, and applications in machining.
- CNC Machining Introduction: CNC lathe/milling components, G-codes, M-codes, coordinate systems.
- Tool Maintenance: Grinding tools, inspecting tool wear, balancing cutters.
- Metrology: Dial gauges, slip gauges, CMM; precision measurement techniques.
- Production Planning: Job scheduling, material estimation, optimizing machining time.
- Machine Maintenance: Lubrication, alignment checks, preventive maintenance for lathes/mills.
Trade Practical
- Grinding Operations: Surface grinding flat plates, cylindrical grinding shafts, dressing wheels.
- Shaping Tasks: Shaping keyways, flat surfaces on shaper, setting stroke length.
- CNC Practice: Setting up CNC lathe/milling, running simple G-code programs (turning, milling slots).
- Tool Care: Sharpening milling cutters, checking grinding wheel balance.
- Precision Measurement: Using dial gauges for runout, slip gauges for height calibration.
- Maintenance Work: Lubricating machine slides, aligning milling table, checking belts.
- Project Work: Machining a precision component (e.g., gear blank) using grinding and CNC operations.
Hours: Theory: 160 hours | Practical: 240 hours
Semester 4
Trade Theory
- Advanced CNC Machining: Multi-axis CNC, tool path optimization, CAD/CAM integration.
- Special Machining: Machining hard materials (stainless steel, titanium), high-precision jobs.
- Troubleshooting: Diagnosing machine faults (vibration, tool chatter), error analysis.
- Automation Trends: Industry 4.0, IoT in machining, smart machine tools.
- Entrepreneurship: Starting a machining workshop, costing, market trends in precision parts.
- Environmental Practices: Recycling metal chips, reducing coolant waste, energy-efficient machining.
- Quality Standards: ISO 9001, Six Sigma, ensuring zero-defect production.
Trade Practical
- Advanced CNC Work: Programming complex shapes (contours, pockets), simulating CAM files.
- Hard Material Machining: Grinding/milling stainless steel, optimizing tool life.
- Troubleshooting Tasks: Correcting CNC errors, fixing milling table misalignment, adjusting clutches.
- Automation Practice: Testing IoT-enabled machine features (e.g., remote diagnostics).
- Field Exposure: Hands-on training in manufacturing units or machining shops (4-6 weeks).
- Quality Inspection: Using CMM for dimensional checks, documenting tolerances.
- Project Work: Producing a complex assembly (e.g., pump housing) using CNC, milling, and grinding.
Hours: Theory: 160 hours | Practical: 240 hours
Additional Components
- Workshop Calculation and Science
- Calculations: Cutting speeds, feed rates, gear ratios, machining time estimation.
- Science: Mechanics of chip formation, friction, thermal effects in machining.
- Hours: 80 hours/year
- Engineering Drawing
- Drawings: Assembly drawings, sectional views, tolerance and fit annotations.
- Hours: 80 hours/year
- Employability Skills
- Communication: Technical reporting, client interaction, teamwork.
- IT Literacy: Using CAD/CAM software, CNC programming tools, online machining resources.
- Soft Skills: Time management, resume writing, interview preparation.
- Hours: 60 hours/year
Assessment and Certification
- Exams:
- Theory: Written exams per semester (MCQs, descriptive questions).
- Practical: Tasks like machining components, CNC programming, grinding, quality checks.
- Evaluation Criteria: Machining precision, tool handling, safety compliance, quality assurance.
- Certification: NCVT National Trade Certificate (NTC) upon passing all semesters, globally recognized.
Career Opportunities
- Employment: Machinist, CNC operator, tool setter in manufacturing, automotive, or aerospace industries.
- Self-Employment: Machining workshop, precision component supplier, tool maintenance services.
- Further Studies: Diploma in Mechanical Engineering, certifications in CNC machining or CAD/CAM.
Trade Type
- 29 views