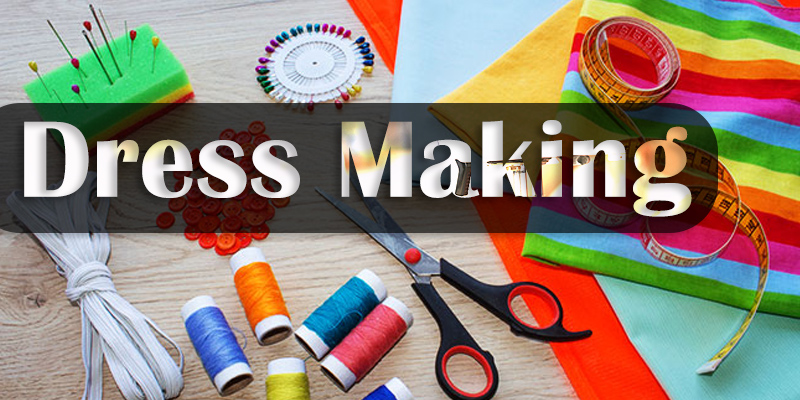
ITI Dress Making Trade Syllabus
The ITI "Dress Making" trade is a one-year vocational training program under the Craftsman Training Scheme (CTS), governed by the National Council for Vocational Training (NCVT). This course equips trainees with skills in designing, measuring, cutting, stitching, and finishing garments, primarily focusing on women’s and children’s clothing. The syllabus integrates theoretical knowledge, practical dress-making skills, and employability training to prepare students for roles such as dressmakers, tailors, or garment production assistants in boutiques, garment factories, or as self-employed professionals.
Course Overview
- Duration: 1 year (2 semesters, each 6 months)
- NSQF Level: Level 4
- Eligibility: Minimum 10th grade pass (or equivalent)
- Objective: To train individuals in dress-making techniques, pattern drafting, and garment construction to produce high-quality apparel that meets market and client demands.
Detailed Syllabus Breakdown
1. Trade Theory (Theoretical Knowledge)
Covers foundational concepts in dress making and garment construction.
- Semester 1
- Introduction to Dress Making
- Overview of the dress-making industry: scope and opportunities.
- Role of a dressmaker: designing, stitching, client consultation.
- Types of garments: women’s wear (saree blouse, salwar kameez), children’s wear.
- Tools and Equipment
- Sewing machines: domestic, industrial – parts, functions, threading.
- Tools: measuring tape, scissors, pins, needles, chalk, rulers.
- Maintenance: cleaning, oiling sewing machines, troubleshooting.
- Fabrics and Materials
- Types of fabrics: cotton, silk, chiffon, denim – properties, uses.
- Fabric selection: suitability for dresses, blouses, skirts.
- Trims and accessories: buttons, zippers, lace, embroidery threads.
- Measurement and Pattern Making
- Body measurements: bust, waist, hip, shoulder, arm length.
- Drafting patterns: basic bodice, skirt, sleeve, collar.
- Pattern layout: marking, cutting, minimizing fabric waste.
- Basic Stitching Techniques
- Hand sewing: running stitch, hemming, backstitch, buttonhole stitch.
- Machine sewing: straight stitch, zigzag, seam finishes.
- Types of seams: plain, French, flat-fell for garment durability.
- Safety and Hygiene
- Workplace safety: handling needles, scissors, sewing machines.
- Personal hygiene: clean attire, hand washing.
- Ergonomics: correct posture for prolonged sewing tasks.
- Introduction to Dress Making
- Semester 2
- Advanced Garment Construction
- Stitching women’s garments: saree blouse, churidar, lehenga.
- Stitching children’s garments: frocks, shorts, party wear.
- Fitting techniques: darts, tucks, pleats for perfect fit.
- Design and Embellishment
- Basic garment designing: sketching dress styles, silhouettes.
- Embroidery: hand and machine embroidery for decorative effects.
- Surface ornamentation: applique, beadwork, sequins for dresses.
- Alterations and Repairs
- Modifying garments: resizing, restyling, adjusting fit.
- Repair techniques: patching, darning, replacing zippers.
- Handling common issues: torn seams, loose buttons.
- Quality Control
- Checking garment quality: stitches, fit, alignment, finishing.
- Identifying defects: uneven hems, loose threads, fabric pulls.
- Ensuring client satisfaction: fit, design, durability.
- Professional Skills
- Client consultation: understanding preferences, body types.
- Entrepreneurship: starting a dress-making business or boutique.
- Market trends: demand for custom dresses, ethnic wear, kids’ fashion.
- Advanced Garment Construction
2. Trade Practical (Hands-On Skills)
Focuses on practical dress-making and garment construction skills.
- Semester 1
- Basic Sewing Practice
- Practicing hand stitches: running, hemming, backstitch on fabric.
- Operating sewing machine: straight, zigzag stitches on samples.
- Sewing seams: plain, French, flat-fell on fabric pieces.
- Measurement and Pattern Making
- Taking accurate body measurements of models.
- Drafting patterns: bodice, skirt, sleeve for simple garments.
- Cutting fabric: laying patterns, marking, cutting with allowances.
- Simple Garment Construction
- Stitching basic garments: apron, baby frock, blouse.
- Attaching components: collars, cuffs, basic buttons.
- Finishing edges: hemming, overlocking for neatness.
- Machine Handling
- Threading and setting up domestic sewing machines.
- Adjusting stitch length, tension for cotton, silk fabrics.
- Cleaning and maintaining sewing machines.
- Project Work
- Constructing a simple garment (e.g., blouse or skirt) from start to finish.
- Documenting measurements, patterns, and stitching process.
- Basic Sewing Practice
- Semester 2
- Advanced Garment Construction
- Stitching women’s wear: salwar kameez, saree blouse, kurti.
- Stitching children’s wear: party frock, school uniform.
- Incorporating fittings: darts, pleats, gathers for shape.
- Design and Embellishment
- Sketching dress designs: casual, ethnic, party wear.
- Practicing embroidery: chain stitch, mirror work on garments.
- Adding embellishments: lace, beads, sequins to dresses.
- Alterations and Repairs
- Resizing garments: taking in or letting out seams.
- Repairing damages: patching tears, replacing buttons.
- Restyling old garments: adding new elements or trims.
- Quality and Finishing
- Inspecting finished garments: checking stitches, fit, aesthetics.
- Correcting defects: re-stitching loose seams, adjusting hems.
- Pressing and packing garments for delivery.
- Project Work
- Designing and stitching a complete garment set (e.g., kurti with palazzo).
- Presenting a report on design, construction, and client suitability.
- Advanced Garment Construction
3. Workshop Calculation and Science
Provides mathematical and scientific support for dress-making tasks.
- Semester 1
- Arithmetic: calculating fabric requirements, seam allowances.
- Measurements: converting inches to centimeters, estimating yardage.
- Geometry: drafting patterns, calculating angles for darts, pleats.
- Semester 2
- Calculations: cost estimation for garments, production time.
- Science: fabric properties (shrinkage, stretch), thread tension.
- Logic: optimizing fabric layout to reduce wastage.
4. Engineering Drawing
Focuses on technical drawing for garment patterns.
- Semester 1: Sketching basic patterns (bodice, sleeve, skirt).
- Semester 2: Preparing detailed diagrams for complex garments (blouse, dress).
5. Employability Skills
Enhances job readiness and soft skills.
- Semester 1
- Communication skills: discussing designs with clients.
- Time management: completing stitching orders on schedule.
- Basic IT skills: recording measurements, order details.
- Semester 2
- Entrepreneurship: planning a dress-making business or boutique.
- Teamwork: collaborating in garment production units.
- Interview preparation: roles in fashion and garment industries.
Assessment and Certification
- Examinations: Conducted semester-wise with theoretical and practical components.
- Certification: Successful candidates receive the National Trade Certificate (NTC) from NCVT, recognized nationally and internationally.
- Evaluation: Based on dress-making skills, garment quality, theoretical knowledge, and project work.
Career Opportunities
- Employment: Dressmaker, tailor, production assistant in boutiques, garment factories, or fashion houses.
- Self-Employment: Starting a dress-making shop, boutique, or freelance tailoring service.
- Further Studies: Diploma in Fashion Designing, Garment Technology, or Costume Design.
Note
- This syllabus aligns with the latest NCVT guidelines and may vary slightly based on institutional or state-specific requirements.
- For the most current version, refer to the Directorate General of Training (DGT) or consult your local ITI.
Trade Type
- 35 views